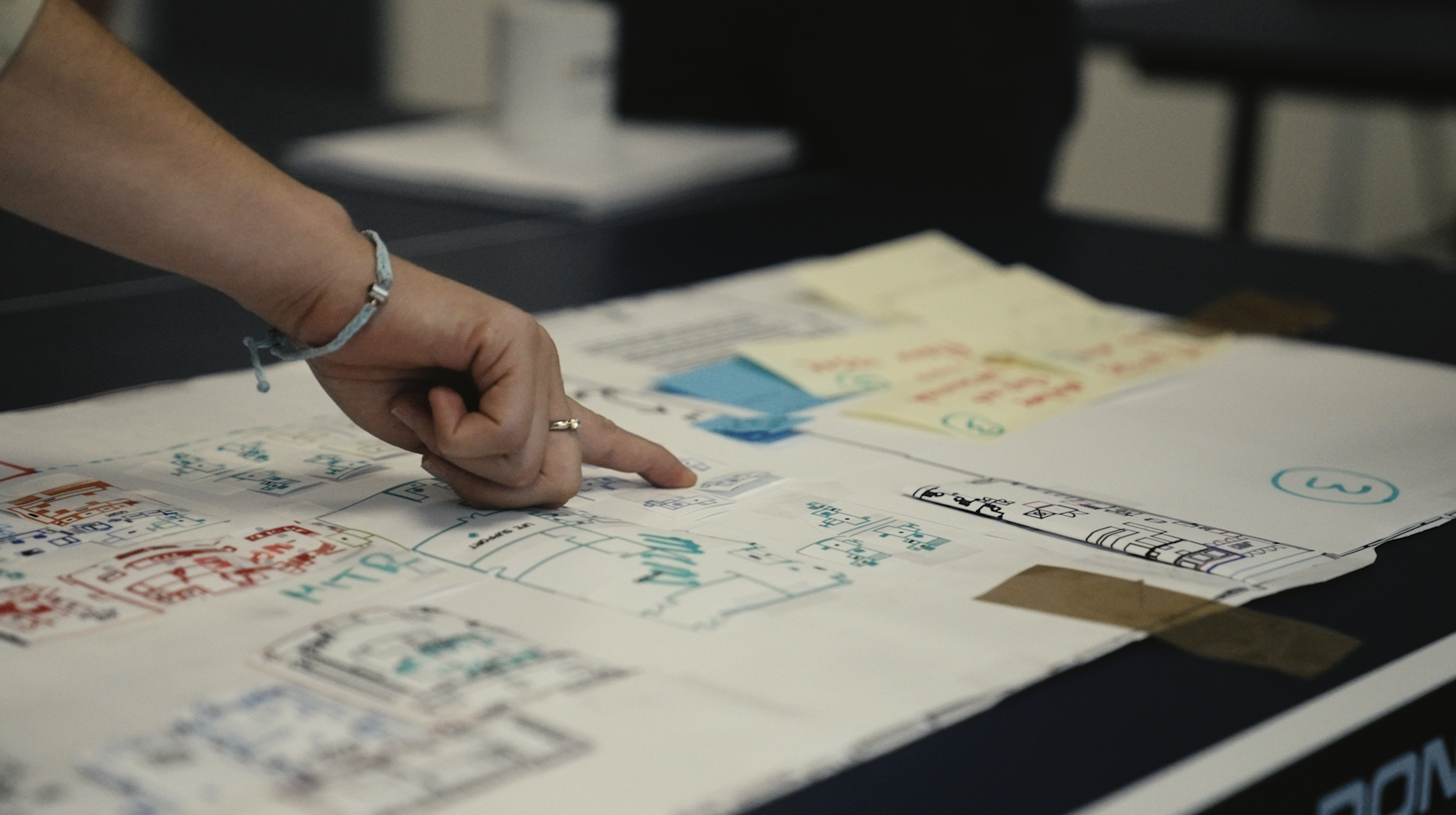
Our approach to Continuous Improvement
We’ve built a culture where improving processes is becoming the Avon way of life, we have much more capable people and the pace of change is accelerating.
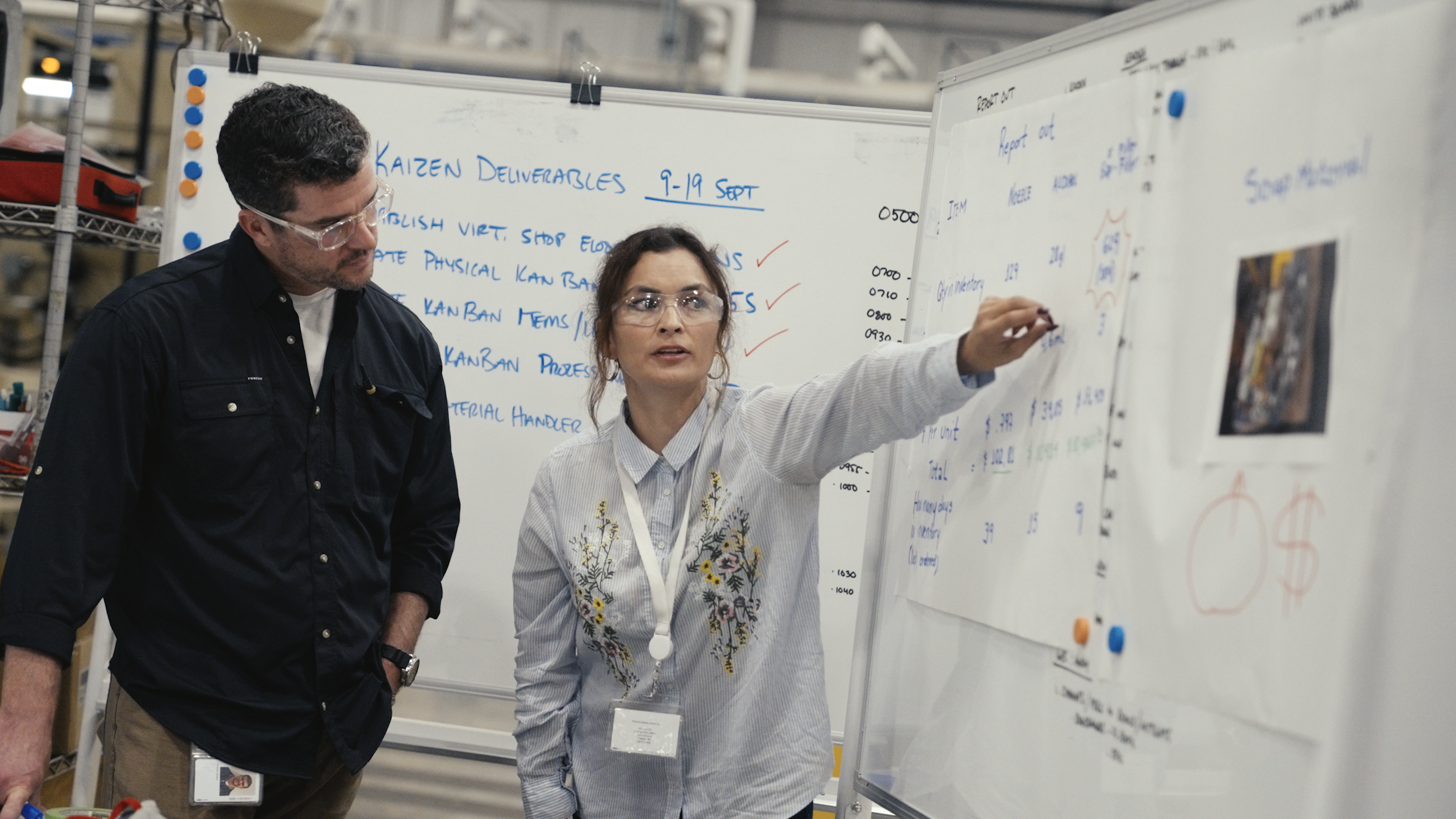
What is Continuous Improvement (CI)?
The aim of CI is to make every process 100% value-adding. At its simplest a business is all about people and processes, and we want those processes to create as much value as possible. We don’t want our employees taking time on things that don’t add value. We can use continuous improvement to look at our processes through fresh eyes. As our people learn to see in a new way, they find the waste in our processes. By taking that waste out, we can focus more on the things that matter.
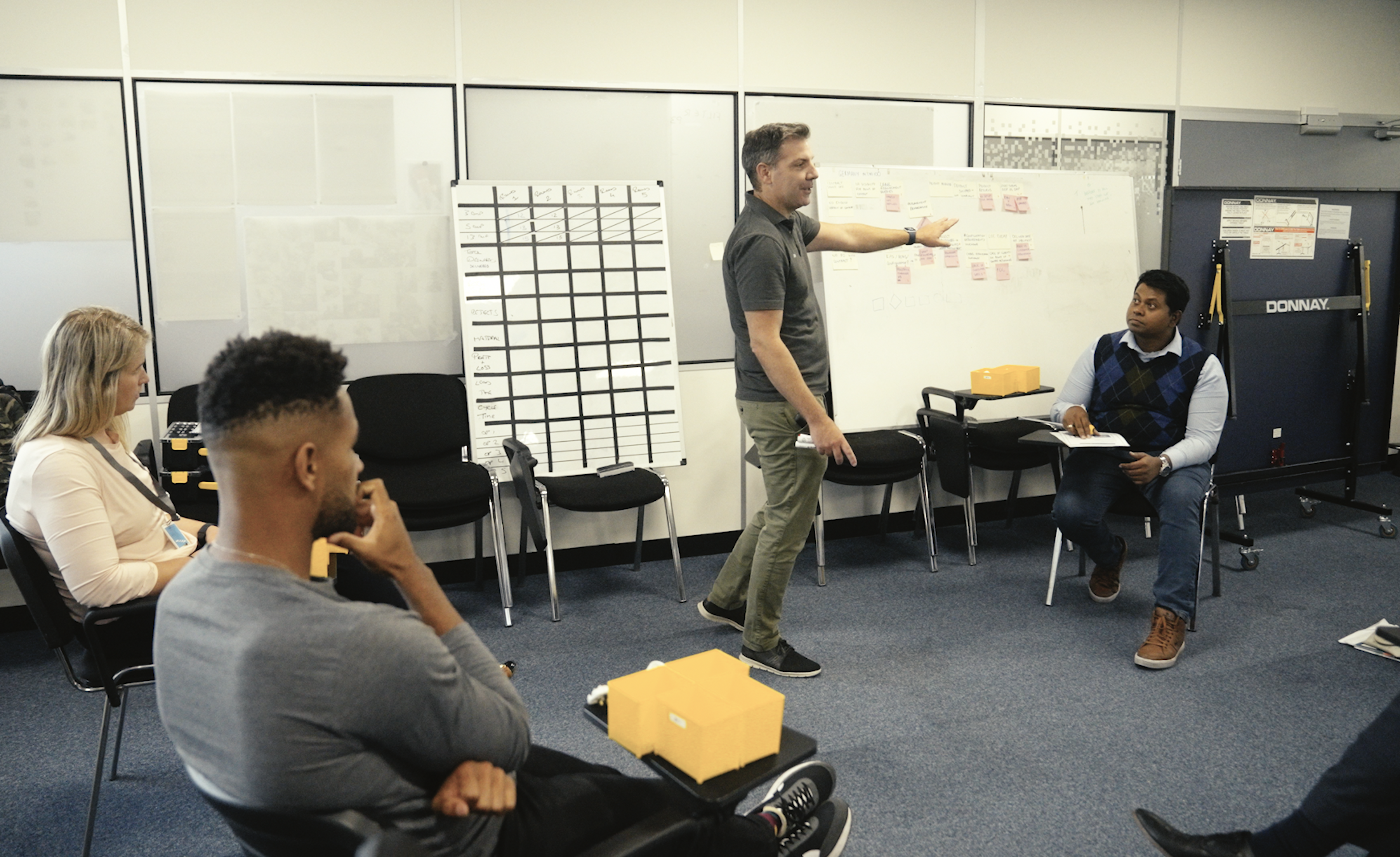
What is Avon Technologies approach to CI?
Continuous Improvement is a critical part of our strategy. At Avon Technologies we translate our strategy into actions which are driven through Kaizen as part of our CI methodology.
We believe that CI will:
- Increase employee happiness and motivation
- Free up cash to invest into the business, funding our transformation programmes and R&D
- Improve productivity, which generates wealth
- Help grow the business by enabling us to reliably deliver quality products with short lead times
How are we doing it?
On the shop floor we aim to dramatically improve our production processes to:
- Achieve one piece flow through our production lines
- Make product to customer demand ('takt time')
- Connect our customers to the shop floor through a pull demand system
- Establish standard work
- Remove waste from the processes and sustain gains
Off the shop floor we aim to:
- Remove waste in the product development process
- Identify waste in the office-based processes and remove it through Kaizen
TARGETS
At the beginning of 2024 we set targets of a 25% productivity increase, a 60% scrap reduction and inventory turns of more than 5 in 2027. We made such good progress in 2024 that we have stretched our productivity and scrap targets to a 35% productivity increase and a >60% scrap reduction.
Versus FY23, at a Group level:
• Productivity improved by 21%
• Scrap reduced by 54%
• Inventory turns improved by 7%
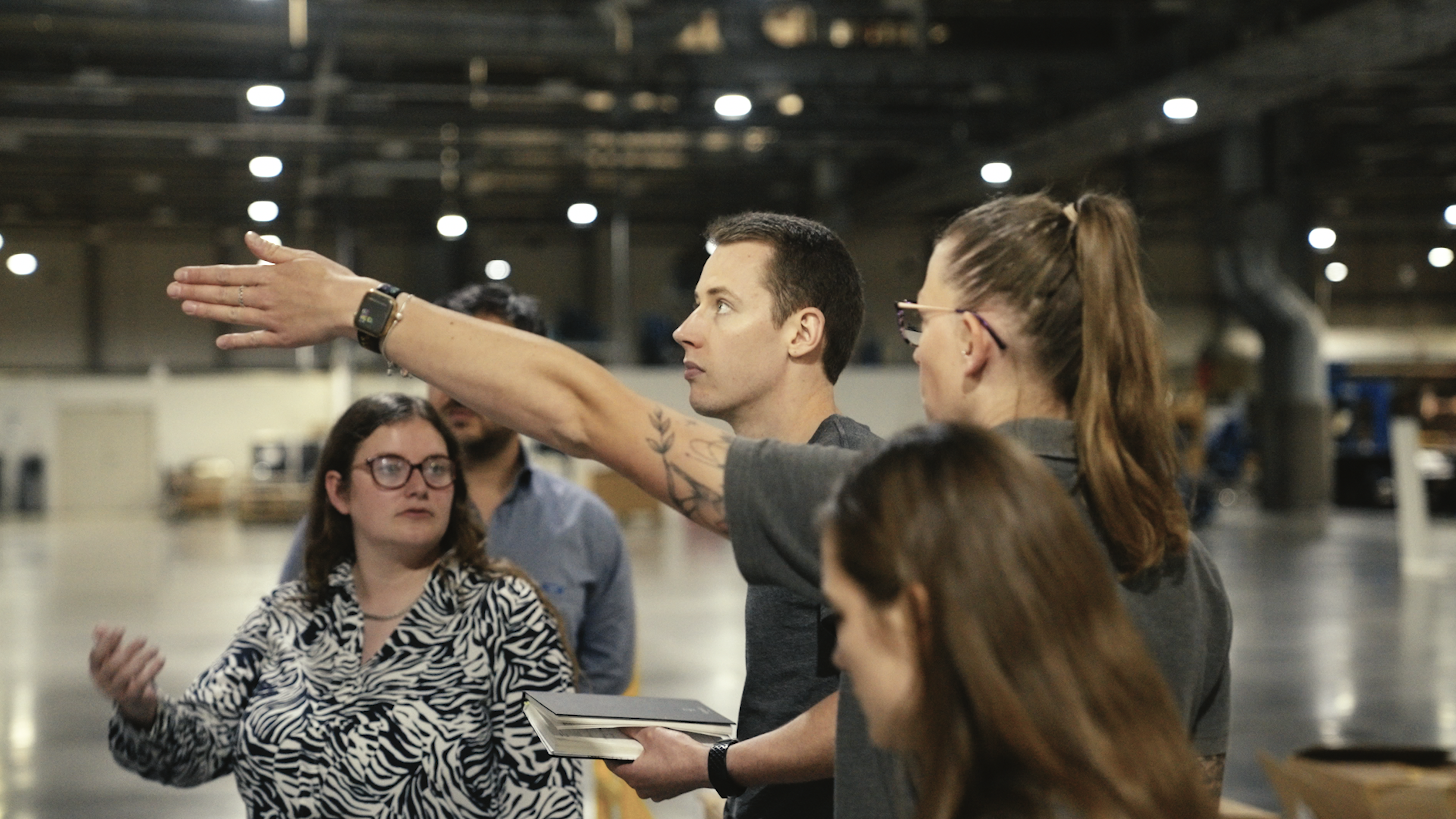
What is Kaizen?
Kaizen literally means make things better. That’s really what continuous improvement is all about; it is trying to make our processes better. At the start of the Kaizen, you have a hypothesis or a charter of what you’re trying to achieve. Then you go straight into doing and you actually try and put into practice your idea and see whether your idea had the effect you wanted.
If it works, then fantastic, you go on to another step, and if it doesn’t work, you still learn something new. Kaizen is not just about what was done and achieved, it’s also about the learnings we get out of it. It’s that experimentation and learning we are embedding into Avon Technologies plc.
How does Kaizen work?
We’re using Kaizen to transform the business, moving from batch production to flow, and developing our employees to identify and challenge waste. Kaizens help foster a culture of “learn by doing” where experimentation is encouraged.
We’re seeing capability being built amongst our employees through Kaizen. Like all skills, the more you do it, the better you are at it and that’s one reason why we’re so keen for there to be so many Kaizens.
Our goal is one Kaizen per week, per plant across the business.
CI in action
CI is all about lots of small actions adding up to make a big impact. See below some case studies showing the impacts of individual Kaizen’s on our production lines:
General Service Respirator
Our recent GSR Kaizen event at our UK facility focused on streamlining production processes and transitioning from a batch production method to a flow model. This transformation significantly improved efficiency, reduced inventory, and optimised operational layouts.
By consolidating production into a single assembly area and integrating quality controls directly into the process, the team achieved remarkable outcomes, including reduced lead times, lower inventory levels, and enhanced productivity. This successful model has since been applied to other production areas at the facility, driving similar transformative results.
A few of many results achieved...
The improvements were significant and transformative:
• 21% improvement in productivity, reducing required operators from 16 to 12
• Lead time cut from four weeks to 91 minutes
• Travel distance reduced from 1,855 meters to just 10 meters per unit
Commercial Helmets
The Kaizen team looked at introducing single piece flow to the assembly cell of commercial helmets in Cleveland. The operators built one mask completely from start to finish within the same station which typically created bottlenecks around the test station. Applying the process balancing method that was simulated during training, the team timed all the individual workstations using standard work combination sheets and plotted these against takt time. Takt time had been calculated previously by the team from understanding customer demands and timeframe ensuring that we only build what the customer requires when they require it.
Focused on driving exponential growth in 2025 and 2026, “Project Osprey” aims to transform Cleveland’s Ballistic Manufacturing Plant into a streamlined operation ready to meet increased demand from the US DOD and commercial markets. Leveraging lean manufacturing principles and a "Yes If" mindset, the plant is being restructured into a cohesive value stream model designed to assimilate ballistic and soft goods production by 2026.
A few of many results achieved…
- Cutting Process Optimisation:
A Kaizen event improved equipment effectiveness from 52% to 74%, consolidating machines, reorganising material flow, and introducing 5S principles. - EPIC, EXFIL, and SL Cell Improvements:
By reconfiguring the layout, standardising work, and reducing operator count, the cell saw a 23% cycle time improvement and a 101% productivity increase, cutting lead times from 14 days to under seven.
These systematic changes have positioned Cleveland's plant to support a significant production ramp-up while improving efficiency, reducing waste, and enhancing flexibility.